Water Nozzle Testing
Applied Impact Robotics - Engineering Intern - Summer 2025
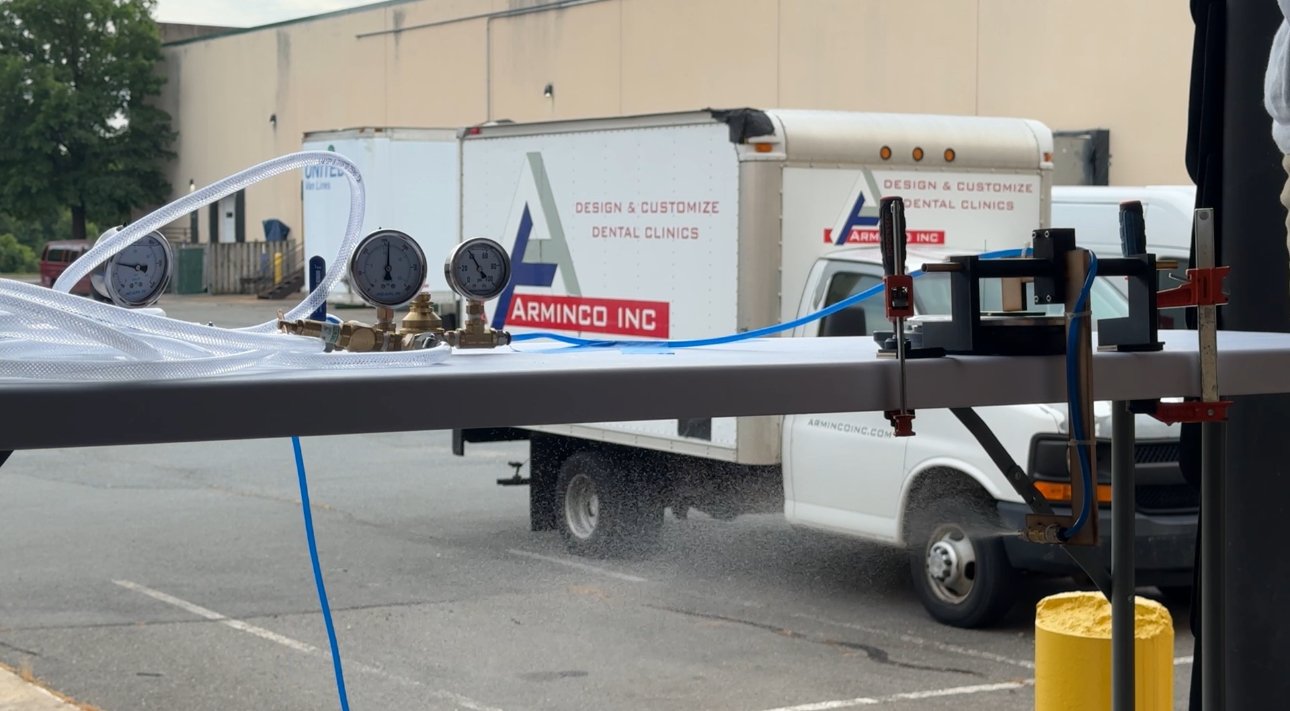
Purpose
There exists on the robot a water nozzle which may impact its functionality*, resulting in the need for testing the force is exerts. Needing my mechanical design fix, I was assigned the task of testing three different water nozzles.
*Propriety, cannot be disclosed in detail
Testing Rig Design
There are many ways to test the force exerted by a nozzle, but given the measurement tools at my disposal, I elected to use a pendulum design.
Components
3D printed:
right and left flanges
rod collars
tightening bearing blocks
2x bearing spacer ring (not pictured)
Laser cut:
pendulum arm
Here is the completed testing rig prior to being hooked up to a bucket of water and the pressure gauge/limiter. The flanges at the very left and right of the rig are clamped down to the table, and the scale (not pictured) sits just under the short end of the pendulum.
Water was fed from a bucket, through an electric pressure washer unit, to a series of pressure gauges and a pressure limiter, which was used to control the pressure, into the hose and to the nozzle.
LEFT: Demonstration of how the pendulum pushes into the scale when the nozzle exerts force.
RIGHT: Demonstration of how pressure was adjusted in 10 psi increments.
When the nozzle sprays, it will rotate the pendulum clockwise about point P, pressing into the scale at the right of the image to the left. Using the equation below, the force interpreted from the mass reading of the scale can be converted to the force exerted by the nozzle.
OTS
2x bearings
300mm aluminum pipe
6501 and 6504 nozzles
1/8” NPT connector
1/8” NPT pushlock
Hose
Testing & Results*
The rig functioned as expected throughout experimentation. Two nozzles were tested, undergoing four trials at six different pressures. The second nozzle was then tested at five more higher pressures with three trials each. I then synthesized the data to provide the force exerted at the nozzle, created a couple of graphs, and presented it to company leadership where it was determined whether the nozzle would impact the robot’s functionality.